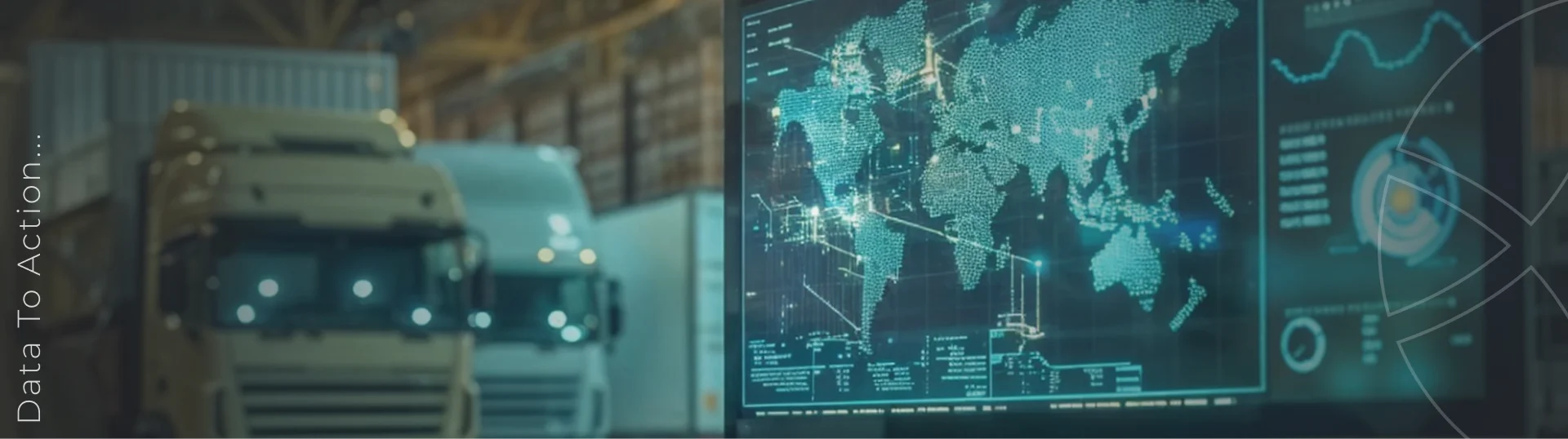
How Advanced Analytics Drives Agility in the Chemical Industry
With nearly 20 million employees and annual sales of about USD 5 trillion, the global chemical industry is massive.
The industry is involved in the manufacturing of several crucial products. It is responsible for converting petroleum and natural gas into intermediate materials, which are then changed into daily-use products.
Many other major industries like agriculture, automotive, pharmaceuticals, and construction industries are dependent on the chemical industry for running smoothly. Hence, any changes in the chemical industry tend to reflect directly on other industries as well.
Thanks to digital transformation, many advanced technologies like artificial intelligence, internet of things, data analytics, big data, and robotics are being explored in the chemical industry.
Employing advanced analytics, in particular, may present some of the biggest opportunities for the chemical industry. Along with gains in manufacturing performance, the chemical industry can also optimise plant operations using advanced analytics.
Many chemical manufacturers already have technologies in place that generate large volumes of data. So, it comes down to utilising the IT systems and infrastructure to take full advantage of the generated data. Chemical manufacturers can use advanced analytics, machine learning, and data visualisation to uncover hidden bottlenecks and optimise plant operations. This can help attain profitable and agile production lines.
In this article, we will discuss how advanced analytics can drive agility and profitability in the chemical industry.
Predictive maintenance to optimize production units
Predictive maintenance is a valuable addition to traditional maintenance methods. As opposed to traditional maintenance programs, a predictive maintenance program can schedule specific maintenance tasks as per the requirement of the plant equipment -before any breakdown happens – thereby reducing the number of unexpected failures.
It analyses data trends and historical performance data of the production units to predict when the equipment is likely to require maintenance. It can then reduce the out-of-service time to bring in efficiency and profitability.
Predictive maintenance can help increase the operating time of critical assets and anticipate their failure. Chemical companies can determine various circumstances that may cause a piece of equipment to break.
By monitoring all the relevant parameters, companies can intervene before the breakage happens and, thus, reduce downtime.
Predictive maintenance has been shown to reduce machine downtime by 30-50% and increase machine life by 20-40%.
The following are the potential benefits that predictive maintenance can offer –
- Cost savings on raw materials
- Reduction of inventory carrying costs
- Improved uptime and equipment availability
- Reduction of maintenance planning
- Reduction in maintenance costs
Yield, Energy, and Throughput (YET) analytics to reduce energy consumption
YET or Yield, Energy, and Throughput analytics can help ensure that the individual production units are running at full efficiency while reducing their energy consumption.
Since even small improvements can affect the profitability of the plant, the fractional gains delivered by YET analytics provide compounded benefits.
Using YET models, one can easily pinpoint fluctuations in any individual components of the manufacturing process. It can help understand performance variations at different locations.
By using YET analytics, companies can create a uniform process and boost agility and profit.
Value-maximisation modeling for higher profitability
Value-maximisation modelling helps scrutinise all the parameters and conditions that affect the profitability of a supply chain. It offers insights from various processes including raw material procurement, purchasing, manufacturing, and sales. These insights can prove valuable in capitalising on the current market conditions.
Value-maximisation modeling can help optimise the interaction between individual pieces of equipment to improve performance and profitability.
This advanced analytics-based technique can show in real-time how to maximise profit generation in complex production systems and supply chains. As opposed to traditional planning, this advanced analytics approach can factor in as many as 10,000 variables and a million constraints to then help chemical producers figure out what to buy, how to make, and what to make, so as to maximise profits.
Detection alarms for increased safety
Since the chemical industry deals with hazardous chemicals, it is essential to continuously monitor the production, transportation, and storage of these hazardous chemicals.
Advanced analytics helps chemical companies monitor these chemicals. It helps in keeping gases like hydrogen, oxygen, sulfide, nitrogen oxide, carbon monoxide, and sulfur dioxide in controlled quantities. This greatly reduces the chances of mishaps and saves life and property.
Advanced analytics for asset management
High asset intensity is a characteristic feature of the chemical industry. Using advanced analytics, companies can improve their asset efficiency. The continuous stream of data collected from various sensors can help asset managers gain a significant advantage over peers who still use traditional data sources.
By employing advanced analytics strategically and sustainably, asset managers can receive enormous value. Other benefits of advanced analytics in asset management are –
- It can help identify the right opportunities
- It can help bring together a set of cross-disciplinary stakeholders
- It can create an environment for testing and experimenting with different strategies
- It can help align the target operating model
Load forecasting for cost reduction
Using advanced analytics, chemical industries can accurately forecast the load of raw materials like water, metals, minerals, oil, etc. This can save a large amount of money for the industry. It also helps meet the demand and supply requirements of power and energy.
Data analytics to build supply chain resilience
Using advanced data analytics, chemical companies can monitor and proactively manage supply chain risks to improve the organisation’s capability of coping with unexpected disruptive events. By utilising data insights, companies can develop mitigation actions and backup plans for critical facilities.
Digital Transformation of the Chemical Industry
Using advanced analytics in the chemical industry has wide implications. It is not just a one-off process but a transformation journey.
The chemical companies that adopt advanced analytics can reap the benefits in the form of improved agility and profitability. Are you ready for the transformation?