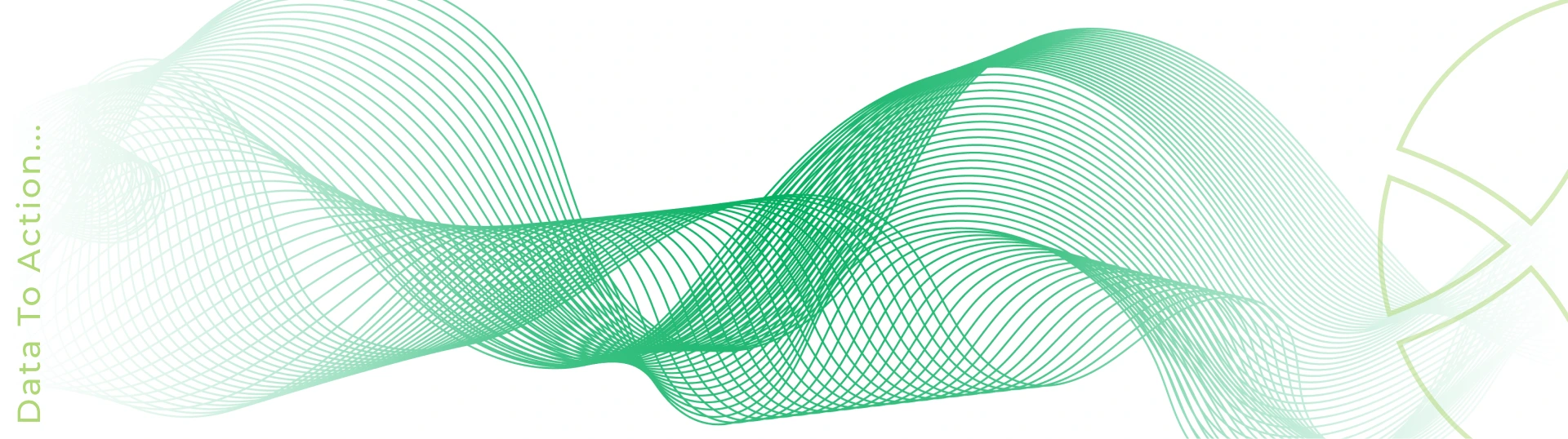
The Art & Science of Data for Industry 4.0
Imagine this – There is a very large area which is extremely clean spotless with PVC flooring. There are numerous rows of machine cabinets and monitors there. A few people in uniforms are going from one machine cabinet to another. They are also monitoring the indicator lamps which flash red or green. What I just described here is not a hospital, but it is the factory hall of Siemens Plant in Germany! This plant manufactures PLCs (programmable logic controls) at the rate of 12 million products per year (which means one unit per second!) Welcome to the world of Industry 4.0. Through optimised automation, Siemens has achieved 75% automation of the value chain at this factory.
If I look back, we have indeed come a long way from the days of the first Industrial Revolution. Did you know that the first Industrial Revolution emerged in the 18th century by the use of water power and steam? The second and third ones launched by the use electricity and introduction of computers subsequently. Now, the fourth industrial revolution, which is much bigger and more revolutionary, is primarily powered by Big Data, the Internet of Things (IoT), Artificial Intelligence, and Cloud Computing.
According to a report published by Price Waterhouse Coopers (PwC), 86% of manufacturers expect to secure simultaneous gains from both lower costs and added revenue in the next five years through their investment in Industry 4.0.
The foundation of the Industry 4.0 revolution is ‘digital trust’. Similar to other industries such as healthcare, retail, FinTech, and automotive, which are looking at digital transformation as the means to dramatically improve their business outcomes, manufacturing is leading the race by leveraging the humongous amount of the data to digitise the entire chain of operations. Today, Japan and Germany are way ahead in this respect but the rest of the world has also woken up to the opportunities presented through digital trust building by leveraging data.
The Focus of Industry 4.0
The focus of Industry 4.0 is on the complete digitisation of existing assets and their integration within the overall digital framework.
- The aim is to perform better analysis through seamless data communication.
- Digitise and integrate digital processes across the organisation – right from operational processes, quality management, product and service offerings to external operations of value service.
- Involve everybody in the value chain – including service partners and customers.
- Gather intelligence from a variety of sources such as IoT platforms, mobile devices, location detection technologies, wearables, augmented reality, smart sensors, big data, etc.
Digital Disruption Fuelled by Industry 4.0
Going digital does not mean only the optimisation of the company operations, it also means the disruption of value chains, entry into newer markets, creation of innovative business models, and achieving superior customer satisfaction. The need for change is fuelled by changing preferences of today’s digital consumer, massive revolutions in technology, changes in the business imperatives, and global competition.
Digital transformation has revolutionised the way manufacturing companies can manage their product innovation, design, engineering, production, and supply chain, through collaboration across geographies. Instead of “doing something digital”, companies have started thinking about “what can be done in digital to derive the real value”.
Here is how Industry 4.0 is set to change the manufacturing industry
- Value Chain Improvement: Connected technologies, sensors, artificial intelligence, robotics, and Cloud are making the data and information exchange smoother and more streamlined and helping manufacturers in deriving a positive impact on the value chain. The ‘physical-to-digital-to-physical’ cycle created by Industry 4.0 has enabled manufacturing companies to focus on the production of physical objects by improving the entire chain – from design, development, manufacturing, sales and service.
- Innovative Product Design and Development: With the use of advanced analytics, artificial intelligence, sensors, 3D scanners, and robotics, manufacturing industries are able to design and develop better products and also able to achieve continuous product improvement by tweaking the product design in a timely manner based on customer and market feedback.
- Enhance Customer Experience: Today, customer experiences are driven by the intelligence gathered from the customer data. This data, when analysed and leveraged properly, helps in enhancing customer interactions by making them hyper-personalised, making marketing and selling of products and services more targeted, and also facilitate smoother post-sales experiences.
- Cost Improvement: By improving productivity, getting rid of redundant processes, improving the production efficiency, and optimising the supply chain, manufacturing companies can improve their overall costs. According to the ‘New Industrial Revolution’ report by Deutsche Bank Research, companies can expect to see a productivity jump of almost 30% through their smart manufacturing initiatives.
Smart Manufacturing Trends to Watch Out
Thanks to smart manufacturing, the manufacturing industry is going through a radical change. Let us take a look at some of the smart manufacturing trends that could further disrupt this industry –
- Robots: With the advancement in technology and as the technology becomes more cost-effective, Robots will become cheaper to procure and program allowing even the small manufacturers to use them. With the maintenance and management of the robots being done by human beings, robots will complement the human workforce. Robots will definitely bring in transformation in the workforce and people will need to acquire specialised skillsets to work along with robots.
- Machine Learning and Artificial Intelligence: Manufacturing companies have started leveraging machine learning and artificial intelligence to enhance their operational efficiency. Machine learning and artificial intelligence are helping in not only automating the assembly lines and enhance the overall productivity but also can be used in product testing and quality control.
- Augmented Reality: With the help of newer technologies such as Augmented Reality, companies are able to quickly create and test products in the virtual world. Right from simulating the design process to the assembly line, everything is possible to be done virtually. This helps in cutting down on manufacturing costs and time, develop products in real-time, and be sure that the product delivers on its purpose.
- Internet of Things: Manufacturing companies are using smart sensors and cloud computing to effectively facilitate communication between machines, record data and feedback, take immediate actions such as device shut off in case of emergency, track production quota, and also manage predictive maintenance. By offering right information at the right time, IoT has enabled real-time decision making – this, in turn, is resulting in cost optimisation, customer satisfaction, and innovation.
It is very clear that as newer technologies such as Machine Learning, IoT, Virtual Reality, Augmented Reality, Cloud, and Big Data become mainstream, the manufacturing industry will leverage these to streamline operations, enhance response times, reduce and downtime, achieve preventive maintenance, drive scalability, increase the output, and translate into greater profits and more jobs.
The mantra for Industry 4.0 seems to be to digitise, industrialise and optimise!
At Inteliment, through our iDS Cloud platform, we are doing our bit in helping the manufacturing industry succeed in its Industry 4.0 initiatives. iDS Cloud is an innovative Data Science platform which helps business users leverage the benefits of data science without the need of data scientists. With iDS, they can easily design workflows, create and reuse predictive models, and run data science – even if they don’t have any technical expertise or data science skills.